"The Organizational Impact of Part Proliferation”
Part proliferation is a reoccurring problem in today’s industry. With a numerous number of parts, companies do indeed have difficulties in controlling product data quality and efficiencies. Here are the areas where Part Proliferation is overlooked, and how to better assess it.
- The costs associated with duplicate part proliferation are not readily apparent nor fully understood.
- The situation is complicated due to non-existing or inadequate search tools and processes that could identify duplicates.
- Short-term deadlines to complete a design take priority ahead of longer-term cost savings from reducing duplicates.
- The implications create issues spanning multiple departments and business units yet often no single department willingly assumes responsibility.
- Since the implications are misunderstood and the responsibility averted, management is often unaware and unable to implement corrective actions.
The Engineering, Purchasing, and Manufacturing departments are typical culprits in contributing to the problem but for their unique reasons.
Engineering
Engineers are good at creating parts and they are typically busy updating their design to meet deadlines.
- From the engineer’s perspective pulling a new part number is usually easy, after all, part numbers are free. Their focus is on the concern at hand, such as completing the design before the next design review. While they may appreciate the implications of duplicates, those costs are more abstract than meeting the looming design deadline.
- Engineers are generally happy to reuse existing proven components, but often finding acceptable existing parts takes too much time. The required part might be in one of many locations, or information about the part might be inconsistent and incomplete. In addition, the search tool might be inadequate in locating and comparing similar parts. When the pressure is on and the time required to find a part is greater than the time to create it, the engineer will inevitably choose simply to create a new part.
Purchasing
After engineering has completed a design, purchasing receives the design’s Bill of Materials to procure parts.
- Purchasing undoubtedly sees duplicates and is aware of how duplicate parts reduce quantity counts for purchases thus minimizing volume-pricing discounts. They are also certainly aware of the processes and challenges required to qualify new vendors of new parts. However, when purchasing receives a Bill of Materials (BOM) and is inundated with parts to purchase, they face time constraints to place orders and meet timelines. Sorting through the BOM and existing inventory to find duplicates is not a priority for the purchasing group.
- The communication between engineering and purchasing is often one-way with engineering not receiving much feedback from purchasing about identified duplicates.
- Making changes to a design is costly for purchasing. Typically, once a BOM goes to purchasing, the design has been released and any changes require a change order. Change orders have substantial costs associated with them since they require additional engineering review and analysis. A change order also incurs time penalties since it will delay the purchase of components and the part build. Therefore, is more cost-effective to make a change order or leave the new part in the design?
Manufacturing
When pulling inventory to assemble products, Manufacturing is likely left wondering why engineering was shortsighted to use duplicate parts.
- Experiencing firsthand pulling duplicate parts from inventory and setting up additional tooling, Manufacturing intrinsically understands the cost of duplicates. New duplicate parts from unproven vendors with different tooling require additional processes and setup time. This introduces variability in manufacturing and inevitably presents new issues in quality. Although Manufacturing experiences firsthand issues with duplicate parts, it is unlikely to rectify the problem for similar reasons as Purchasing.
- Communication between manufacturing and engineering is often not bi-directional and suffers from an “over-the-wall” mentality.
- Manufacturing typically has its own list of issues to contend with without adding the elimination of duplicate parts to the list.
- Uncertainty exists for Manufacturing since it is unclear if an engineer specified a near duplicate part for a specific reason. It is not always obvious and often there is insufficient part data to perform an effective component comparison. For example, a near duplicate part may have exact dimensions, but a different indistinguishable coating for operating in hostile environments.
- Eliminating duplicates or near-duplicate parts requires Change Orders, requiring time, which costs money and delays delivery of the product.
How to Increase Awareness about Duplicate Part Proliferation
What can be done to increase awareness about part duplication?
- Ensure that everyone understands the multiple ways duplicate parts can increase costs across the entire lifecycle of a product. Educate Engineering, Purchasing, and Manufacturing about the issues and costs associated with duplicate part proliferation.
- Improve communication between Engineering, Manufacturing, and Purchasing. Incorporate Purchasing and Manufacturing early in the design process and ensure there is effective feedback to Engineering about duplicate parts. Identify duplicate parts before releasing a design to avoid the expense of a Change Order.
- Since the issues of duplicate part proliferation exist over multiple departments and divisions, it is often overlooked. Make Management aware of the problem and assign responsibility to manage duplicate part proliferation. Some companies have created specific roles (commonly referred to as Component Data Specialist) to manage part proliferation.
- Implement a data governance program to maintain high-quality part data and a New Part Introduction (NPI) process. This will introduce a review and comparison of existing components before creating a new part.
- Provide tools to effectively classify components and efficiently search and compare existing parts.
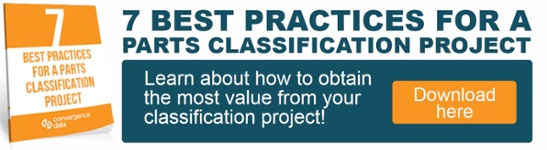